When growing a brand new electrical powertrain for Components E, a number of goals have to be balanced and prioritised. Energy, effectivity and controllability are all essential for producers, and compromise is inevitable when figuring out the very best total package deal. A extremely environment friendly powertrain is of little use if it can’t attain most energy rapidly sufficient, has an excessive amount of inertia, or lacks the required software program controls for vitality administration.
Every of those core parts additionally entails extra concerns, highlighting the intensive work required to carry a undertaking from idea to the monitor. Since Components E started a decade in the past, and powertrain improvement was opened up in season two, a number of facets of the design and improvement course of have matured massively. We now have extra information and higher instruments than we did again then.
Proof of this may be seen within the inverters, which convert DC present from the battery into AC present for the motor. The inverters are actually over 99% environment friendly, and the electrical motors we use are greater than 98% environment friendly. This excessive degree of improvement can largely be attributed to enhancements in motor building, electronics precision and velocity, and advances in supplies science, leading to elevated {hardware} capability.
When Components E first started with a typical powertrain able to 150kW in race mode, we used a five-speed gearbox as we couldn’t obtain most energy early sufficient. My crew, Abt Sportsline, diminished this to 3 gears in season two, two gears in season three, and ultimately one gear in season 4.
Eliminating a number of gears was a significant breakthrough within the Gen1 period as gear shifts end in time loss and damage effectivity. Now, each crew makes use of a single gear, which requires particular therapies for the gear tooth. These tooth are made huge and shallow to scale back friction, which improves effectivity and permits the vehicles to speed up seamlessly from 0-300km/h.
Within the first season of Components E, groups used five-speed Hewland gearboxes, however when powertrain improvement was opened up the main target turned to eliminating a number of gears
Photograph by: Mark Sutton
Arguably the most important distinction between previous and current improvement lies in advances in software program calculations and predictive engineering. These spectacular developments enable for extra exact simulations of actuality, streamlining the event course of and enabling quicker innovation. As an alternative of manufacturing a number of powertrain iterations and testing them bodily to search out the very best resolution, a lot of the optimisation can now be completed just about earlier than components are manufactured.
So, what are the principle standards we search for in a Components E powertrain? First, it’s important to realize most energy throughout all revs as early as doable. We’re restricted to 350kW, so the motor should function at its peak with out exceeding that restrict, which might end in a penalty. Energy management is difficult, notably when the motor, gearbox and driveshaft oscillate over kerbs or bumps.
A throttle map that delivers torque easily is a key space the place the motive force can affect improvement. I deal with how the motor behaves underneath braking, how its positioning impacts the automotive’s steadiness, and optimising software program controls, like how the motor responds to regenerative braking.
A bigger motor with thicker copper wiring sometimes has much less resistance. Nevertheless, a bigger motor additionally means extra mass and weight
Incremental features in effectivity are a steady space of focus. We’re at all times in search of an additional 0.1% or 0.2%. The vital factor is attaining effectivity throughout the whole package deal, not simply within the motor and inverter.
Along with excessive peak effectivity, we intention for top common effectivity, which requires a big motor. A bigger motor with thicker copper wiring sometimes has much less resistance. Nevertheless, a bigger motor additionally means extra mass and weight, so different elements should even be thought-about. Lightness has clear advantages for effectivity, and low inertia can be crucial.
Putting the fitting steadiness is a posh job that at all times requires compromises, however the advances revamped the previous 10 years have been really outstanding.
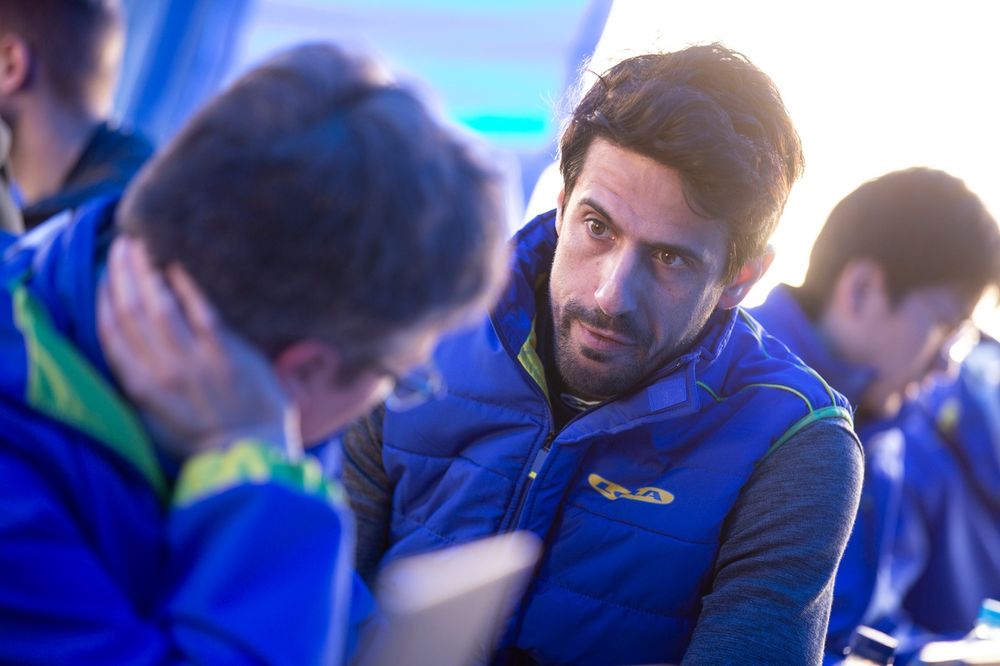
Di Grassi is now a key cog within the improvement of latest Lola/Yamaha Components E powertrain that will probably be utilized by Abt subsequent season
Photograph by: Lola